XV. Indicadores de Desempenho
Valor Económico Acrescentado (EVA)
EVA = R - D - I - CC
Onde:
EVA = Valor Económico Acrescentado
R = Receitas
D = Despesas
I = Impostos
CC = Custo do Capital
Para aumentar o EVA pode-se aumentar o lucro, aumentando as receitas e/ou diminuindo as despesas e o custo do capital. Então:
O aumento das receitas é obtido, principalmente, aumentando a satisfação do cliente, por exemplo, produzindo o que os clientes querem, no momento em que querem;
Para diminuir as despesas / custos, pode-se começar por identificar e eliminar todas as actividades que não adicionam valor ao produto final (actividades de valor não acrescentado). Outra maneira é substituir stocks ou transportes, que envolvem recursos físicos, por informação;
Para diminuir os custos do capital, pode-se reduzir os empréstimos e optimizar a utilização dos activos.
Duas empresas que tenham o mesmo lucro operacional líquido podem ter EVA´s completamente diferentes, uma empregando mais capital ou tendo mais despesas com empréstimos do que a outra.
As empresas que conseguem, com sucesso, analisar todos os processos internos para formar uma Cadeia de Abastecimento que a diferencie, aos olhos dos clientes, podem conseguir uma redução média de 10 a 15% dos custos de encomenda, 10 a 20% dos custos de posse de stocks e 5 a 10% dos custos de transporte (Nogueira, 2006).
Indicadores AECOC
A AECOC (2003) recomenda indicadores para o nível de serviço logístico num documento dividido em três secções: introdução, indicadores de eficiência e indicadores de serviço.
Na introdução são referidos os objectivos dos indicadores e que para cada indicador são identificados os seguintes itens: definição; fórmula geral; fórmulas alternativas, se as houver; quem pode medi-lo; frequência de medida; e razões para a análise dos resultados.
O indicador de eficiência tem como objectivo medir o nível de Aplicação da Ficha de Recomendações AECOC para a Logística (RAL), como base da eficiência entre clientes e fornecedores:
Aplicação da Ficha RAL (%) =
= (Facturação com a Ficha RAL / Total da Facturação) × 100,
com a facturação medida ao preço de venda.
Fórmulas alternativas,
avaliação realizada pelo cliente:
= (Número de Fornecedores com a Ficha RAL / Número Total de Fornecedores) × 100,
avaliação realizada pelo fornecedor:
= (Número de Clientes com a Ficha RAL / Número Total de Clientes) × 100.
Os indicadores de serviço recomendados são as Entregas a Tempo, Entregas Completas, Qualidade da Entrega / Recepção e Tempo de Descarga.
O indicador Entregas a Tempo mede o nível de cumprimento do compromisso da data e hora de entrega acordada entre o fornecedor e cliente, com uma margem de ± 15 minutos:
Entregas a Tempo (%) =
= (Número de Encomendas Entregues a Tempo / Número Total de Encomendas Entregues) × 100.
As Entregas Completas permitem conhecer o nível de cumprimento da entrega das quantidades encomendadas pelo cliente ao fornecedor:
Entregas Completas (%) (unidades de consumo) =
= (Número de Unidades Recebidas / Número Total de Unidades Encomendadas) × 100.
Entregas Completas (%) (linhas da encomenda) =
= (Número de Linhas da Encomenda Recebidas / Número Total de Linhas da Encomenda) × 100.
A Qualidade da Entrega / Recepção permite conhecer o nível de ocorrências no acto de entrega / recepção,
medida pelo cliente:
Encomendas com Ocorrências (%) =
= (Número de Linhas da Encomenda com Ocorrências / Número Total de Linhas da Encomenda) × 100,
medida pelo fornecedor:
Encomendas com Ocorrências (%) =
= (Número de Encomendas Devolvidas Total ou Parcialmente / Número Total de Encomendas) × 100.
O último indicador recomendado é o Tempo de Descarga, que tem por objectivo determinar o nível de cumprimento de um compromisso de duas horas ou menos. O tempo de descarga é o tempo que decorre desde a entrega da documentação à chegada, até à saída das instalações do cliente com a documentação já assinada. À chegada o tempo começa a partir da hora acordada, nos casos de chegadas anteriores à hora acordada.
Encomendas Descarregadas a Tempo (%) =
= (Número de Encomendas Descarregadas em duas horas ou menos / Número Total de Encomendas Entregues) × 100.
Todos os indicadores recomendados devem ser medidos com uma frequência mensal (Figueira, 2006).
Taxa de Rotação dos Stocks
A taxa de rotação dos stocks é usada para avaliar a eficiência com que os gestores utilizam os seus investimentos em stocks. A Figura 15.1 ilustra o conceito de taxa de rotação dos stocks.
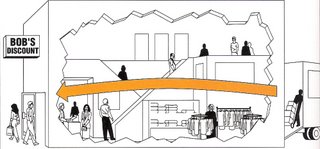
Fonte: Levy e Weitz, 2004
A taxa de rotação dos stocks é «mercadoria em movimento». Os artigos são entregues no cais do armazém, nas traseiras do hipermercado, passam algum tempo nos expositores até serem vendidos e saiem pela porta da frente do hipermercado. Quanto mais rapidamente se desenrolar este processo, maior será a taxa de rotação dos stocks. Pode-se interpretar a taxa de rotação dos stocks como sendo o número de vezes que, em média, os stocks circulam pelo hipermercado durante um certo período de tempo, normalmente um ano. É uma medida da produtividade dos stocks, ou seja, permitem saber qual a receita líquida que foi gerada por cada UM investida em stocks.
A taxa de rotação dos stocks é calculada pelas seguintes relações matemáticas:
Taxa de rotação dos stocks = Receita líquida anual / Valor do stock médio a preços de venda
ou
Taxa de rotação dos stocks = Custo dos bens vendidos anualmente / Valor do stock médio a preços de custo.
Como a maior parte dos retalhistas tendem a pensar nos stocks a preços de venda, a primeira expressão é preferível. Aritmeticamente, pode não haver diferença entre os valores calculados pelas duas fórmulas. O importante é tanto o numerador como o denominador serem expressos a preços de venda ou de custo.
Suponha-se que as vendas anuais foram de 100 000 UM, com uma margem de 40% e o custo médio dos stocks 33 333 UM. Então
Taxa de rotação dos stocks = 100 000 (1 - 0,40) / 33 333 = 1,8
(Prazeres, 2006)
Os indicadores que se seguem baseiam-se numa recolha do texto de White (1985), sobre Medidas de Desempenho, feita por Virgílio A. P. Machado, enquanto Professor - Visitante, no Departamento de Engenharia Industrial da Texas A&M University, em College Station, no ano lectivo de 1992 / 93.
Indicadores de Utilização de Recursos: Pessoas
= Pessoal destacado para tarefas de movimentação de materiais / Total de pessoal operativo
ou
= Movimentação de materiais indirecta anual, $ / Total da folha de pagamentos anual, $
[proporção]
Este indicador avalia a utilização de pessoal na movimentação de materiais e representa o número de pessoas destacadas para tarefas de movimentação de materiais em relação a toda a força laboral. Pode ser determinado com base no número de trabalhadores a tempo inteiro ou nos custos da folha de pagamentos. Normalmente, a movimentação de materiais indirecta inclui operadores de equipamento de movimentação de materiais a tempo inteiro (veículos, gruas e trabalho manual), actividades relacionadas (operários de cais, empregados do armazém e de limpeza) e actividades de apoio (manutenção, ferramentaria, registos de controlo de existências, controlo da produção e trânsito). Muitas das actividades de apoio não são dedicadas a tempo inteiro à movimentação de materiais. Se uma pessoa não desempenhar uma tarefa de movimentação de materiais a tempo inteiro, deve ser utilizada uma estimativa da percentagem do tempo gasto em movimentações, sendo a percentagem apropriada determinada por amostragem do trabalho.
Este indicador deve ser inferior a 1, um valor razoável deve ser inferior a 0,3 numa fábrica e um valor normal pode ser de 10%, enquanto que num armazém é de esperar um valor mais elevado. Algumas possibilidades de melhoria incluem a redução do número de movimentações necessárias.
= Tempo despendido em movimentação de material pela mão de obra directa, h / Tempo total de mão de obra directa, h
ou
= Mão de obra directa de movimentação de materiais, $ / Mão de obra directa total, $
[proporção]
também conhecido por
Nem toda a movimentação de materiais é efectuada por mão de obra indirecta; daí a utilização deste indicador. Geralmente é desejável que tenha um valor baixo, já que «a mão de obra da produção é para se concentrar na produção». O tempo que a mão de obra directa gasta em movimentação de materiais é determinado por amostragem estratificada por departamento e talvez até por operário. Um valor normal pode ser de 14%. Algumas possibilidades de melhoria incluem levar os materiais ao operador em vez do operador ao material e dispor as máquinas de modo a que uma pessoa possa trabalhar com várias máquinas (Figueira, 2006a).
Indicadores de Utilização de Recursos: Equipamentos
= Produção real / Capacidade teórica
= Itens movimentados por hora / Capacidade teórica
= Peso da carga movimentada por hora / Capacidade teórica
= Cargas movimentadas por hora / Capacidade teórica
= Produção real / Produção teórica
= Movimentação real por dia / Capacidade diária de movimentação
ou
= (Velocidade de movimentação, % do «padrão») (Peso movimentado, % do «padrão»)
[proporção]
também conhecido por
Utilização de Equipamento de Movimentação
Desempenho da Movimentação
A maneira como este indicador é determinado varia de uma instalação para a outra. Portanto, só tem significado se for usado para fazer comparações relativas, durante um período de tempo, para uma dada operação. Para usar este indicador adequadamente, deve-se decidir o que significa capacidade teórica – ou utilização total – e manter essa definição. Por exemplo, pode-se considerar um equipamento totalmente utilizado só quando transporta uma carga completa. Por outro lado, pode-se achar que está a ser utilizado adequadamente quando vazio mas a dirigir-se para um posto de carga.
Idealmente, o indicador deve estar próximo de 1,0; contudo, avarias do equipamento, má calendarização, manutenção deficiente e a geografia do edifício podem reduzir o movimento de cargas.
No formato de produto, este indicador é determinado por amostragem do trabalho e decisão. O equipamento é observado; o observador avalia a velocidade do equipamento como uma percentagem da velocidade «padrão» para essa situação e o peso movimentado como uma percentagem do peso «padrão» que pode ser movimentado.
Algumas possibilidades de melhoria incluem a colocação de acopladores nas empilhadoras que permitam a utilização de várias acessórios, o despacho em tempo real de camiões no sentido de reduzir a quantidade de deslocações improdutivas e a grupagem de ordens de trabalho.
= (Número de observações a trabalhar / Número total de observações) × 100
[percentagem]
Dependendo dos desejos da organização, a trabalhar pode ser definido como a movimentação de uma carga completa, movimentação de uma carga parcial ou completa, ou movimentação com carga ou vazio, ou a trabalhar pode até incluir a carregar / descarregar. Organizações diferentes usam definições diferentes de a trabalhar, por isso as comparações entre organizações devem ser feitas com cuidado. Se a percentagem de ocupação está acima de 75% para veículos e gruas, então é provavelmente muito elevada para estes equipamentos de «serviço aleatório»; é de considerar a utilização de equipamentos de percurso fixo tais como correias transportadoras ou veículos sem condutor (Figueira, 2006b).
= Tempo de funcionamento / Tempo total
= Tempo de funcionamento / ( Tempo de funcionamento + Tempo parado)
= Fiabilidade / (Fiabilidade + Manutenção)
= Tempo médio entre falhas, h / (Tempo médio entre falhas + Tempo médio de reparação, h)
[proporção]
Muitas vezes, o custo mais importante é um custo de mão de obra – o operador. O custo de manutenção também é principalmente um custo de mão de obra. Então a solução é manter o operador ocupado, isto é, maximizar a disponibilidade e minimizar o custo de manutenção. Isto é conseguido com equipamento fiável (poucas avarias ou elevado tempo médio entre falhas) e com equipamento reparável (reparações rápidas ou baixo tempo médio de reparações). A manutabilidade, medida como o tempo médio de reparação, geralmente exclui a manutenção fora das horas de produção. A disponibilidade pode não ser a reparação rápida de um veículo que avaria. Muitas empresas mantêm veículos sobresselentes (mais máquinas que homens). Outras arrendam ou alugam, por um curto período de tempo, de um fabricante, enquanto a unidade avariada é reparada.
Apesar de muitas empresas terem registos de manutenção elaborados, muitas não os têm: é difícil e dispendioso manter registos correctos. Se existem registos de manutenção, devem fazer-se por veículo e não só globalmente. Uma decisão chave é equipar cada veículo com um tacógrafo. As leituras dos tacógrafos são melhores indicadores de quando substituirdo que os meses do calendário.
= Número de máquinas ou postos de trabalho executando operações na peça em consideração, planeadas de maneira a poderem ser deslocadas, para um novo local na mesma linha de produção, num turno de trabalho / Número total de máquinas ou postos de trabalho a efectuarem operações na peça em consideração, na linha de produção
[proporção]
Este índice é usado satisfatoriamente como uma medida da flexibilidade das máquinas de uma linha de produção em relação ao fluxo da peça. Uma máquina é um aparelho não portátil com uma fonte de energia separada ou individual. Um posto de trabalho é a área coberta pelas ferramentas, equipamento, máquinas e materiais em curso de fabrico necessários para o desempenho de uma dada operação.
= Número de máquinas ou postos de trabalho na área em consideração, projectadas de maneira a poderem ser deslocadas, para qualquer outro local, num turno de trabalho / Número total de máquinas ou postos de trabalho na área em consideração[percentagem]
Este índice é uma medida útil da disposição das máquinas e postos de trabalho em termos da utilização de homens e máquinas (Figueira, 2006c).
Indicadores de Utilização de Recursos: Espaço
= Espaço de armazenagem ocupado por materiais, m3 / Espaço total de armazenagem disponível, m3
ou
= Volume ocupado por materiais ao nível máximo normal de armazenamgem, m3
/ Espaço total de armazenagem disponível, m3
ou
= (Espaço total de armazenagem disponível, m3 - Espaço de armazenagem ocupado por materiais, m3) / Espaço total de armazenagem disponível, m3
[proporção]
também conhecido por
Utilização do Espaço de Armazenagem
Eficiência da Utilização do Espaço de Armazenagem
Eficiência da Utilização do Espaço
Utilização do Volume de Armazenagem
Este índice é uma excelente medida da utilização do volume dos espaços de armazenagem ou armazéns, tais como a recepção e expedição, onde, obviamente, esta medida vai ser aplicada mais frequentemente. É uma medida potencialmente boa da adequação da embalagem, paletização ou movimentação de materiais, tal como aplicada a sistemas de armazenamgem. Dá, também, uma indicação verdadeira da utilização global da área da instalação para armazenagem de material em curso de fabrico ou das ferramentas e equipamento necessário para modificar estes materiais. Reflecte, prontamente, um aumento ou diminuição do espaço de armazenagem. Deve ser medida o volume em vez da área para encorajar o uso da dimensão vertical.
Ter o cuidado de medir a situação real, em vez de trabalhar com desenhos. Ao recolher os dados, registar a percentagem de contentores e espaços das prateleiras que estão vazios. Dos que estão ocupados, anotar se estão a ser total ou parcialmente utilizados e estimar a percentagem de utilização que deve ser incluída nos cálculos.
Um valor perto de 1 (ou 0, na fórmula alternativa) indica a atribuição de espaço apropriado para as actividades de armazenagem. Se o indicador de armazenagem for muito elevado, contudo, vai haver dificuldades em aceder ao material. Algumas possibilidades de melhoria incluem a armazenagem aleatória, em vez de dedicada.
= (Volume ocupado pelos corredores, m3 / Volume total, m3) × 100
[percentagem]
também conhecido por
O espaço está a tornar-se extremamente caro, tanto na produção como na armazenagem. Corredores e tipos de tráfego devem ser desenhados cuidadosamente de modo a usar, da forma mais produtiva, o volume disponível. Os cálculos devem, geralmente, ser feitos em m3 em vez de m2 para encorajar o uso da dimensão vertical. Os corredores podem ser cobertos com armazenagem por cima dos corredores de cruzamento. Este indicador dá uma indicação verdadeira da utilização global do volume de armazenagem par corredores. Um aumento ou diminuição no volume dos corredores reflecte-se, prontamente, num aumento ou diminuição do valor deste indicador. Deve ter um valor entre os 10 e 15%, embora as condições particulares de produção encontradas determinem se é desejável um valor alto ou baixo. Tenha-se, também, em mente que um valor demasiado baixo pode ser tão mau como um que é muito elevado. Se o valor é demasiado baixo, vai haver problemas de acesso aos materiais. Um número razoável de tráfego e corredores de acesso devem estar disponíveis para manter níveis desejáveis de movimentações e produtividade. Ter o cuidado de medir a situação real em vez de trabalhar com desenhos. Algumas possibilidades de melhoria incluem corredores estreitos (menos de 2,4 metros) e mezzanines sobre actividades de baixo pé-direito.
= [(Volume actual dos corredores, m3 – Volume óptimo teórico dos corredores, m3) / Volume actual dos corredores, m3] × 100
[percentagem]
Este índice dá uma indicação do volume usado em corredores que se pode poupar, para utilizar para outros fins, como percentagem do volume que está a ser usado, actualmente, em corredores.
= [(Comprimento máximo da máquina, m + 0,6) × (Largura máxima da máquina, m + 0,6) + Área de trabalho do operador, m2] / [Área total da instalação, m2 – (Área total de corredores, m2 + Área total ocupada por materiais, m2)]
[proporção]
Este índice é uma indicação rigorosa da eficiência com que a área da instalação é utilizada. Aqui, máquina significa toda a maquinaria de produção, incluindo correias transportadoras assentes ou perto do chão, mas excluindo correias transportadoras elevadas que passam por cima e sem tocar noutra maquinaria. Deve-se salientar o facto de que as áreas ocupadas por máquinas, postos de trabalho e operadores podem ser totalmente independentes umas das outras; isto é, uma área de trabalho de produção pode consistir de máquinas ou postos de trabalho operados por trabalhadores, ou de máquinas a operar independentemente, ou de trabalhadores a operarem independentemente. O chão pode ser ocupado por armazenagem temporária ou controlada de materiais, ou por ferramentas e equipamento necessário para modificar estes materiais (Figueira, 2006d).
Indicadores de Utilização de Recursos: Energia
= kWh / Volume, m3
[kWh / m3]
também conhecido por
Mais do que nunca, todas as pessoas estão preocupadas com a eficiência energética dos equipamentos e operações, podendo utilizar os indicadores que cobrem este importante factor. Pode ser possível determinar as diferentes eficiências energéticas – relacionando a movimentação com o consumo de energia – para equipamentos individuais tais como as correias transportadoras ou empilhadoras. Contudo, uma avaliação mais significativa pode ser a energia utilizada para toda a instalação, medindo a eficiência das operações de aquecimento e arrefecimento – por exemplo kWh / m3 do espaço de armazenagem. Para operações em escritórios com pé direito baixo e consistente, pode-se querer calcular por m2 em vez de por m3. A tabela seguinte mostra os factores de conversão de vários tipos de combustíveis para kWh. A unidade comum é o kWh em vez de UM para eliminar o efeito da inflação e permitir comparações com instalações com diferentes taxas de serviços de utilidade pública. Um BTU consumido por dia é igual a 7,033 706 Wh.
Este indicador pode ser mantida baixo com medidas tais como: fornecendo aquecimento, ventilação, ar-condicionado e iluminação em áreas sem pessoal ou instalações de armazenagem automática a níveis apropriados para produtos, em vez de para pessoas, fechando as cabines dos veículos, desligando as lâmpadas quando não são necessárias, iluminando as tarefas com projectores ou luzes montadas em equipamentos móveis, em vez de iluminação superior permanente, colocando as lâmpadas do tecto por cima dos corredores, em vez de por cima dos produtos e usando microprocessadores para regular o consumo de energia.
Se a fonte de energia for | e as unidades são | para ter as unidades em kWh, |
multiplicar por | ||
Carvão betuminoso | Kg | 8,069 |
Energia eléctrica | KWh | 1 |
Gás natural | m3 | 10,347 |
Gasóleo | litro | 8,825 |
Gasolina | litro | 7,8 |
Óleo combustível n.º2 | litro | 9,09 |
Oléo combustível n.º4 | litro | 9,49 |
Propano | Kg | 13,889 |
Vapor (comprado) | Kg | 0,646 |
= Somatório das distâncias verticais em que é utilizada a alimentação por gravidade numa instalação com vários pisos, m / Distância vertical total, para cima ou para baixo, que um componente percorre, envolvendo esforços, quer mecânicos, quer humanos, desde a área de entrada até à área de saída da configuração de uma instalação com vários pisos, m
[proporção]
Este índice pode ser considerado uma boa indicação da medida em que a gravidade é utilizada para movimentar peças para cima e para baixo. Quando aplicado operações num único piso, dá resultados peculiares e pouco razoáveis (Figueira, 2006e).
Indicadores de Controlo de Gestão: Materiais
= (Tara, kg / Peso bruto, kg) 100 [percentagem]
= (Tara, kg / Capacidade de carga, kg) 100 [percentagem]
= Tara, kg / Volume bruto, m3 [kg / m3]
= Tara, kg / Volume utilizável, m3 [kg / m3]
= Capacidade de carga, kg / Volume bruto, m3 [kg / m3]
= Capacidade de carga, kg / Volume utilizável, m3 [kg / m3]
= Capacidade de carga, kg / Área interior, m2 [kg / m2]
= (Volume utilizável, m3 / Volume bruto, m3) 100 [percentagem]
= Volume utilizável, m3 / Custo, $ [m3 / $]
Os indicadores acima podem ser interpretados em termos de famílias de curvas por tipos de contentores e também é possível interpolar a partir dessas curvas ou gráficos em situações em que os dados reais não estão disponíveis (Figueira, 2006f).
Indicadores de Controlo de Gestão: Movimentação
= Número total de movimentações de um produto, movimentações / Número total de operações de transformação de um produto, operações
[proporção]
Esta relação reflecte a eficiência global das operações de movimentação de materiais numa instalação. Pode indicar o número de actividades de movimentação – e removimentação – envolvidos na recepção, armazenagem, produção e noutros departamentos. Normalmente, um indicador elevado indica uma oportunidade de melhoria, na forma de menos actividades de movimentação, operações simplificadas, ou utilização de equipamento mecanizado.
= Total da distância de movimentação, m / Número total de movimentações de um produto, movimentações
[m / movimentações]
O número de movimentações e distâncias são normalmente desenvolvidos em fluxogramas. Os dados, especialmente para as distâncias, devem ser medidos como são feitos e não como imaginados numa mesa do escritório. Algumas possibilidades de melhoria incluem diagramas de fluxo para o material, equipamento e pessoas, e o desenvolvimento de configurações alternativas para reduzir distâncias.
= Distância que um componente ou peça tem que percorrerdurante a produção, m
[m]
Este não é propriamente um indicador, mas simplesmente um número de metros. É uma boa medida da eficiência com que a rota da produção está configuradada e pode ser usada para comparar instalações ou áreas produzindo o mesmo tipo de produto. Determinou-se ser mais preciso que qualquer indicador analisado.
= Somatório das distâncias que um componente se movimenta automaticamente de máquina para máquina, sem movimentação externa de materiais, m / Distância real total que um componente percorre na rota da produção desde os armazéns de matérias-primas até aos de produto acabado, m
[proporção]
A movimentação externa de materiais significa movimentação manual de materiais da produção de um local para outro, em caixas, tabuleiros e afins. No âmbito de organizacões mais pequenas, a distância real total que um componente percorre na rota da produção desde os armazéns de matérias-primas até aos de produto acabado, pode ser reformulado como: a distância desde a entrada da área do layout até à saída da área do layout.
Este indicador tem sido consistente e preciso e é recomendado como uma boa medida da eficiência da rota de produção em relação à mecanização da movimentação de materiais (Figueira, 2006g).
Indicadores de Controlo de Gestão: Perdas
= Número de cargas danificadas / Número total de cargas
[proporção]
Este indicador dá uma ideia de como as equipas de pessoal movimentam efectiva e apropriadamente as mercadorias que entram e saem, e os materiais em curso de fabrico. O indicador mede a qualidade do desempenho do pessoal de movimentação de materiais. Os requisitos de controlo das perdas podem ser exemplificados por «no máximo, são danificados 3 a 5% dos produtos movimentados» e «o custo dos bens danificados varia de 5 a 50 vezes o custo dos acidentes de trabalho».
As cargas danificadas devem ser determinadas por amostragem e não por relatório do próprio operador. Qualquer componente danificada de qualquer produto é considerada uma carga danificada. O indicador deve ser determinado para diferentes departamentos e fases do fluxo de materiais na instalação, tais como recepção, fabricação e expedição. A danificação das cargas durante a recepção, movimentação em curso de fabrico e expedição devem ser minimizados, Algumas possibilidades de melhoria incluem a instalação de aspersores e detectores de fumo, e fazer com que operadores da movimentação de materiais recebam treino formal, com refrescamento periódico.
= Investimento verificado em stocks, $ / Investimento esperado em stocks, $
[proporção]
A perda por contracção dos stocks deve-se a furtos, erros de registo e de expedição, entre outros. Algumas possibilidades de melhoria incluem fazer com que as pessoas que entram e saem do edifício passem por uma passagem apertada com vigilância humana (Figueira, 2006h).
Indicadores de Eficiência Operacional: Produção
= Tempo de máquina, h / Período de tempo, h
= Somatório de todos os tempos de ciclo de operações de produção, h / Período de tempo no ciclo de produção, h
[proporção]
Este indicador mede a eficiência com que os materiais circulam no processo de fabrico. Obviamente que se podem esperar valores diferentes entre operações à tarefa e sistemas de processamento contínuos. O tempo de máquina inclui todo o tempo gasto nas operações de produção reais nas máquinas, tratamentos e inspecção, incluindo tempo de carga/descarga. O período de tempo é desde que a unidade entra no departamento de produção (por exemplo, 08h00 de 4 de Junho) até sair (por exemplo, 09h00 de 20 de Junho). Só contam os dias úteis e apenas 8 h/dia (assumindo que um turno é de 8 h), então neste exemplo, o período de tempo seria 12 dias × 8 h/dia + 1 = 96 + 1 = 97 h.
O tempo não gasto na produção pode ser causado por atrasos na movimentação de material, má programação e rota, operação ineficiente das máquinas e falha das máquinas, e limitações da armazenagem, entre outras razões. Para aumentar a utilização das máquinas, o atraso deve ser eliminado ou pelo menos minimizado. O indicador de desempenho deve ser aplicado e observado constantemente, durante um certo tempo.
Algumas possibilidades de melhoria incluem ter sistemas de identificação automática para melhorar a entrada de dados de controlo dos materiais, padronizar métodos de movimentação de materiais e contentores, e considerar tecnologia de grupo e configuração em células. (Note-se, contudo, o conflito entre a tecnologia de grupo, que recomenda a produção de artigos da mesma família em conjunto, e o Planeamento de Recursos Materiais (MRP II), que recomenda a produção de artigos só imediatamente antes de serem necessários.)
= Número de tarefas atrasadas numa semana, tarefas/semana / Número de tarefas completadas numa semana, tarefas/semana
[proporção]
Não dar demasiada importância às tarefas atrasadas. Apesar dos atrasos serem de evitar, não devem ser evitados a qualquer preço.
= Soma das percentagens do tempo de paragem das máquinas para todos os casos em que as percentagens individuais de tempo de paragem são iguais ou menores que 50% dos ciclos de trabalho individuais / (100 Número total de operadores dessas máquinas)
[proporção / operador]
Esta razão é um indicador preciso da eficiência obtida agrupando máquinas para operações com várias máquinas. Deve-se notar que é usado só quando a porção do tempo de máquina do ciclo total de trabalho é automático e as máquinas podem ser deixadas a trabalhar sozinhas. O tempo de paragem é a proporção do ciclo de trabalho em que a máquina é carregada e descarregada.
= Somatório das percentagens do tempo de paragem das máquinas para todos os casos em que as percentagens individuais de tempo de paragem são maiores que 50% dos ciclos de trabalho individuais / (100 Número total de operadores dessas máquinas)
[proporção / operador]
Este critério é semelhante ao indicador principal acima, excepto que só é usado para grupos de máquinas diferentes a que o índice principal não se adapta (Figueira, 2006i).
Indicadores de Eficiência Operacional: Armazenagem
= Linhas de encomendas separadas por dia, linhas/dia / Horas de trabalho por dia, h/dia
[linhas/dia]
Dependendo da aplicação, o tempo de separação de uma encomenda pode ser só o tempo para separação da encomenda ou pode incluir também o tempo de reposição e embalagem.
Algumas possibilidades de melhoria incluem a avaliação da separação de uma única encomenda versus separação de várias encomendas versus separação por zona; a avaliação da movimentação do empregado até ao artigo versus movimentação do artigo até ao empregado; e a avaliação de armazenagem dedicada (cada referência com um local próprio sempre lhe atribuído) versus armazenagem aleatória (referência armazenada em qualquer local) (Figueira, 2006j).
Indicadores de Eficiência Operacional: Recepção e Expedição
= Peso recebido (expedido) por dia, kg/dia / Horas de trabalho por dia, h/dia
[kg/h]
ou
= Cargas recebidas (expedidas) por dia, paletes/dia / Horas de trabalho por dia, h/dia
[paletes/h]
ou
= Volume recebido (expedido) por dia, m3/dia / Horas de trabalho por dia, h/dia
[m3/h]
Existem muitas oportunidades de melhoria na recepção e expedição. Parte do desafio consiste no facto do trabalho ser grandemente influenciado pelos vendedores e fornecedores, e pelos departamentos utilizadores internos. Isto é, muito além do controlo do supervisor local e carece de uma abordagem sistémica.
Algumas possibilidades de melhoria incluem a programação da chegada e partida dos camiões, sistemas de identificação automática, impressoras de etiquetas e digitalizadoras para facilitar a introdução de dados e reduzir os erros, e transportadores extensíveis que entram nas caixas ou atrelados dos camiões (Figueira, 2006k).
Valor da Mão de Obra Directa
Nas oficinas de uma empresa de hipermercados, procedeu-se, durante seis meses, à recolha de dados refentes ao trabalho de um mecânico. Estes dados permitem comparar as horas de presença remunerada com as horas de trabalho efectivo registadas nas folhas de serviço.
Meses (i) | 1 | 2 | 3 | 4 | 5 | 6 |
Horas de presença (Ti) | 176 | 160 | 176 | 160 | 184 | 160 |
Horas de trabalho efectivo (ti) | 167 | 144 | 169 | 155 | 169 | 144 |
Índice de eficiência médio: ∑ ti / ∑ Ti = 948 /1 016 = 0,933
em que i = 1, 2, 3, 4, 5, 6
O mecânico recebe por hora de presença 24 UM. Na realidade, a sua hora de trabalho fica por
24 × (1 / 0,933) = 25,72 UM
Para o cálculo de um preço de custo, há que ter em conta o custo real da mão de obra e não o custo contabilístico. Neste exemplo, a diferença é significativa e foram, posteriormente, imputadas à má organização das oficinas.
Há, contudo, que não confundir o índice de eficiência, exclusivamente relacionado com a organização do trabalho, com o índice de rendimento relativo ao trabalho do operário e que é um problema totalmente diferente (Rosemberg, s.d. e Gorgulho, 2006d).
Suponha-se, por exemplo, dois vencimentos: 3 000 UM e 6 000 UM. Admita-se que o escalão da Segurança Social se situa nas 4 000 UM.
Para o primeiro vencimento, o conjunto das cotizações aplicar-se sobre 3 000 UM, ou seja:
5 00 UM × (0,35 + 0,15) = 1 500 UM
Para o segundo vencimento, o cálculo efectua-se de uma forma diferente:
4 000 UM × 0,35 = 1 400 UM
6 000 UM × 0,15 = 900 UM
Total = 2 300 UM
A relação
(encargos sociais) / vencimentos
indica, para ambos os vencimentos:
1 500 / 3 000 = 50%
2 300 / 6 000 = 38,33%
É, por isso, prudente conhecer-se previamente a estrutura dos vencimentos, antes de se aplicar um qualquer coeficiente multiplicador dos encargos sociais (Gorgulho, 2006e).
Referências
AECOC - Indicadores RAL de Nivel de Servicio, «Recomendaciones AECOC para la Logística (RAL)», Barcelona, 2003. Consultado a 25 de Março de 2006.
LEVY, Michael; WEITZ, Barton A. - Retailing Management, 5.ª ed, Boston, McGraw-Hill Irwin, 2004.
NÓBREGA Júnior, Joaquim Inácio Campos - Metodologia para Análise Estratégica de Projectos de Cadeias de Abastecimento Industriais. Florianópolis, Universidade Federal de Santa Catarina, 2000.
ROSEMBERG, Claude - Análise de Custos, Rentabilidade e Produtividade. Porto, Rés, s.d.
WHITE Jr., John A. - Management Guide to Productivity, in ROBESON, James F.; HOUSE, Robert G., eds., «The Distribution Handbook», Nova Iorque, The Free Press, 1985, p. 319 - 369.
0 Comments:
Post a Comment
<< Home